3.5 mm Precision Connectors
To ensure measurement accuracy, use 3.5 mm precision connectors. However, you can use SMA connectors if special care is taken when mating the connectors, and all connectors are undamaged and clean. Before each use, check the mechanical dimensions of all connectors with a connector gauge to make sure that the center conductors are positioned correctly. Remember, all connections must be made for consistent and repeatable mechanical (and therefore electrical) contact between the connector mating surfaces. Carefully study and practice all procedures in this topic until you can successfully perform the procedures repeatedly. Accuracy and repeatability are critical for good high frequency measurements.
Precision 3.5 mm Microwave connectors are compatible with an SMA connector within its specification. Due to the variable quality of the SMA connector, mating with an SMA can sometimes cause severe damage to the 3.5 mm connector.
The device connection procedures differ in several important ways from traditional procedures used in the industry. Keysight Technologies have developed the following procedures through careful experimentation.
Protecting Input Channels
The Keysight N9355CK01 is a DC coupled limiter (DC to 26.5 GHz) that is used to protect sensitive oscilloscope channels from damage due to electric overload stress (EOS) and electrostatic discharge (ESD). For example, voltages in excess of ±2V can damage high-performance samplers used in oscilloscopes. The limiter dramatically reduces the likelihood that such voltages will reach the sensitive part of the instrument, ensuring that the oscilloscope will perform reliably. Instruments with dual electrical channels, such as the 54754A, will require two N9355CK01 limiters. Step generators within the TDR modules use
≤0.2V, which is less than the diode threshold of the N9355CK01 limiter. The N9355CK01 can also be used to protect the electrical channel of the 86105x and similar modules, as long as the signal does not exceed –0.5V to +0.5V. The N9355CK01's voltage drop is ±0.6V to 0.7V at ±10 mADC.
The N9355CK01 will protect instruments from occasional and short voltage spikes. A major power source, such as a high voltage and current supply can still cause severe damage to the limiter itself, or the instruments. Operators should continue using industry standard EOS and ESD practices to minimize this risk.
Figure. Two N9355CK01s Inserted into TDR Module Signal Paths
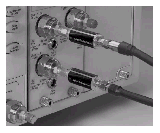
Visually Inspecting 3.5 mm Connectors
You must always begin a calibration with a careful and thorough visual inspection of the connectors, including the test set connectors, to ensure they are not damaged.
Ensure that you and your equipment are grounded prior to touching any center conductor so you will not produce static electricity and create a potential for electrostatic discharge. When using or cleaning connectors, be aware that you are touching exposed center connectors that are connected directly to the internal circuits of the oscilloscope. Touching the center conductor, especially with a wiping or brushing motion, can cause an electrostatic discharge and severely damage these sensitive circuits.
Use an illuminated, 4-power magnifying glass for visual inspection.
- Examine the connectors for obvious problems, such as deformed threads, contamination, or corrosion.
- Examine the mating surfaces of each connector. Look for scratches, rounded shoulders, misalignment, or any other signs of wear or damage.
- Ensure that the surfaces are clean, free of dust and solvent residues. Dirt or damage visible with a 4-power magnifying glass can cause degraded electrical performance and possible connector damage.
- Repair or discard all damaged or worn connectors.
Mechanically Inspecting 3.5 mm Connectors
After you perform a visual inspection of the precision connectors, you must perform a mechanical inspection. This inspection consists of using the appropriate male or female precision 3.5 mm connector gauge to check the mechanical dimensions of all connectors, including those on the test set. The purpose of this inspection is to ensure that perfect mating will occur between the connector surfaces. Perfect mating assures a good electrical match and is important to avoid damaging the connectors themselves, especially on the instrument.
Center Conductor
The critical dimension to be measured is the recession of the center conductor. No protrusion of the center conductor's shoulder is allowable on any connector. The maximum allowable recession of the center conductor shoulder is 0.003 in. (0.08 mm) on all connectors, except those on the channel connectors. On the channel connectors, not only is no protrusion allowable, the shoulder of the center conductor must be recessed at least 0.0002 in. (0.005 mm). The maximum allowable recession of the center conductor shoulder on the channel connectors is 0.0021 in. (0.056 mm).
Outer Conductor
If any contact protrudes beyond the outer conductor mating plane, the contact is out of tolerance and must be replaced. If the center conductor is not recessed at least 0.0002 in. (0.005 mm), it is out of tolerance and must be replaced. In both cases, the out-of-tolerance connector will permanently damage any connector attached to it. Destructive electrical interference will also result due to buckling of the female contact fingers. This is often noticeable as a power hole several dB deep occurring at about 22 GHz.
If any contact is recessed too far behind the outer conductor mating plane (0.0021 in. 0.056 mm, except in test sets), poor electrical contact will result, causing high electrical reflections. Careful gauging of all connectors will help prevent this condition.
Before using the connector gauge to measure the connectors, visually inspect the end of the gauge and the calibration block in the same way that you inspected the connectors. Dirty or damaged gauge facings can cause dirty or damaged connectors. Two connector gauges are available from Keysight Technologies, one for each connector type, male and female. A single gauge calibration block is used to zero both gauges; one end protrudes for zeroing the male connector gauge. The part number for both gauges, as well as the calibration block is 85052-80010.
Type-N connectors can be tightened hand tight, but for better repeatability they should be torqued to 135 N-cm.
The 5/16" head of the 8710-0510 wrench will need to be ground thinner for some applications.
NMD connectors are rugged test port or cable connectors.
A 56 N-cm. torque wrench should be used to connect male SMA connectors to either 3.5-mm or 2.92-mm connectors. A 90 N-cm torque wrench should be used to connect male 3.5-mm or male 2.92-mm connectors to mating female connectors.
Disconnecting 3.5 mm Connectors
To disconnect, follow this procedure:
- Loosen the connector nut on the male connector with the torque wrench. Leave the connection finger tight.
- While supporting the calibration device, gently unfasten the connectors and pull the calibration device straight out of the channel connector. Do not twist either the center conductor or the outer conductor housing or exert lateral or vertical (bending) force on the connection.
Some precision 3.5 mm female connector fingers are very tight and can pull the center pin of their mates out past specifications when the connectors are disconnected. If such a male pin is inserted into a female connector, it can cause considerable damage by pushing the female center conductor back too far. Be aware of this possibility and check all connectors before mating them again.